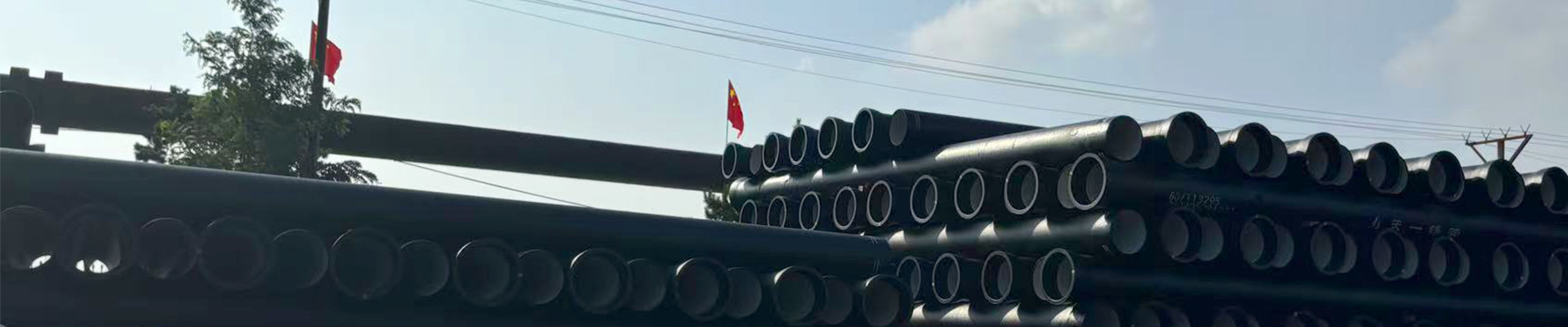

Preparation of hot metal
Blast furnace ironmaking: The quality of hot metal is closely related to the composition of raw materials. Our company tests each batch of raw materials, refines low-phosphorus and low-sulfur hot metal, and ensures that the content of carbon, phosphorus and sulfur in the hot metal meets the requirements.
Tempering of hot metal: The medium-frequency electric furnace uses advanced analysis and perfect process control during the tempering process to ensure the stability of the hot metal composition. Hot metal spheroidization: Hot metal produced by the electric furnace is spheroidized with a spheroidizing agent to adjust the composition to meet the process requirements.
Hot metal quality control: The weight and temperature must be strictly controlled at every stage of the hot metal preparation process. Each furnace of hot metal must be analyzed by a spectrometer to ensure that the hot metal fully meets the requirements of centrifugal casting.
Centrifugal casting
Centrifugal casting: Our company uses the water metal process for centrifugal casting. The molten iron at about 1360C after melting in the electric furnace is continuously poured into the high-speed rotating pipe mold, and the molten iron is solidified by water cooling to form a ductile iron pipe. Quality control: The cast ductile iron pipe is immediately inspected for casting defects on the surface to ensure the quality of the centrifugally cast ductile iron pipe.
Annealing: The qualified ductile iron pipe then enters the annealing furnace with full computer temperature control, and is fully annealed to obtain the metallographic structure required for ductile iron.
Performance testing: The annealed ductile iron pipe is immediately subjected to appearance inspection, hardness test, pressure ring test, metallographic test and tensile test, and the pipe that does not meet the requirements will be scrapped.


Finishing
Weighing: Use electronic scale to weigh each ductile iron pipe to ensure that the weight of the pipe meets the quality standard requirements. Zinc spraying: In order to further enhance the corrosion resistance of ductile iron centrifugal cast iron pipes, zinc spraying is required on the outer surface of the pipe. Metal zinc spraying is used, and the material is metal zinc with a zinc content of more than 99%. The weight of the zinc layer is not less than 130g/m', and the weight of the zinc layer in any area is not less than 110g/m'. To ensure the quality of zinc spraying, zinc spraying should be carried out after the heat treatment process is completed and the pipe body itself is still at a certain temperature.
Grinding: When qualified zinc-sprayed ductile iron pipes are sent to the grinding station, the internal and external surface defects are inspected, and the sockets of each pipe are polished and cleaned.
Hydrostatic test: Our company conducts hydrostatic test on each ductile iron pipe in accordance with the national SO standard. Once leakage occurs, the cast pipe will be scrapped immediately. We guarantee that all cast iron pipes are not welded or glued. Cement internal coating: The zinc-sprayed ductile iron pipe is centrifugally sprayed with cement on the inner wall of the pipe by a cement internal coating machine. The cement slurry used has undergone strict quality inspection and ratio control. The internal coating process of the ratio is fully computer-controlled to ensure stability. Curing: After spraying cement lining, the ductile iron pipe will be cured in accordance with strict corporate standards. Asphalt spraying: After internal coating curing, the zinc-sprayed ductile iron pipe is sprayed with imported asphalt paint to increase the corrosion resistance of the ductile iron pipe. Inspections are carried out every shift, and the coating thickness is not less than 70 microns.